特色产业领航 绘就外贸发展新画卷
特色产业领航 绘就外贸发展新画卷
特色产业领航 绘就外贸发展新画卷新华社(xīnhuáshè)北京6月9日电 题:工业“关节”里的硬核突围——老(lǎo)企业洛轴创新蝶变启示录
在中(zhōng)国工业版图中,有这样一家企业,用轴承“转动”大国重器(zhòngqì)、“转”出市场话语权——
洛轴集团,前身是国家“一五”期间156个重点建设项目之一,70多年深耕(shēngēng)轴承制造,自研自制的多个产品打破了长期依赖进口的局面(júmiàn),高端轴承产值占企业总产值比重达(dá)70%。
近年来,随神舟飞船叩问苍穹,伴盾构机掘地潜行,助海上风机(fēngjī)发出绿电,洛轴始终(shǐzhōng)向新而进,把“卡脖子”短板一点点变成可以参与国际竞争的长板,老企业的突围给人(rén)启示、引人深思。
这是5月24日拍摄的洛轴集团智能工厂(gōngchǎng)生产线(无人机照片(zhàopiān))。新华社记者 李嘉南 摄
做产业链的“填空者(zhě)”
夏日洛阳(luòyáng),地铁疾驰,呼啸而过。新装配洛轴轴承的(de)地下“巨龙”,在中原大地(dàdì)的土壤中穿行。迄今,这辆洛阳地铁2号线0217车已安全行驶24万公里。
2022年4月,洛轴启动实施地铁(dìtiě)车辆轴箱轴承自主化研制项目,历时两年完成装车运用(yùnyòng)考核试验,伴随着(zhe)“洛轴造”一路应用,地铁产业链国产化的“关键拼图”不断补齐。
轴承,工业的“关节”,作为机械设备的核心基础零部件(língbùjiàn),直接影响着装备制造能力,关系着国家工业水平(shuǐpíng)。
产业大厦不能建在别人的(de)地基之上。特别是盾构机、载人飞船等重大装备领域,要打破国外企业的垄断,造出质量、精度要求(yāoqiú)极高的轴承。“补短板”之路,历经几多(jǐduō)艰辛、几多坎坷。
6月(yuè),骄阳似火。洛轴(luòzhóu)技术中心,为满足跨海隧道等重大工程建设的需要,新一代12米以上超大直径盾构机轴承工业技术和工程应用研究正(zhèng)如火如荼地展开。
穿越山海(shānhǎi)的重器,勾起跨越时间的记忆。
“人家说,你们拿回去吧(ba),就算不要钱,我们也不敢用(yòng)。”想起过去推销盾构(dùngòu)机主轴承的经历,洛轴集团盾构机主轴承设计师周琳五味杂陈。
盾构机技术先进、附加值高。在长达(zhǎngdá)数十年的时间里,世界上仅有几家公司掌握这样的能力,主轴承资料都被严密(yánmì)封锁。设计、制造、润滑、试验……洛轴(luòzhóu)历尽(lìjìn)千辛万难,好不容易研发出来的产品,在市场面前却不堪一击。
另辟蹊径,2012年开始,周琳(zhōulín)和团队联系盾构机厂家,提出以低价承担使用过程中的检修工作,从(cóng)一个小滚动体(tǐ)开始,从查找缺陷、修复问题切入,一点点摸索验证。
盾构机深埋地下,闷热潮湿。4年间(niánjiān)100多套轴承(zhóuchéng)检修下来,周琳已记不清经历了多少(duōshǎo)个被汗水浸透(jìntòu)的日夜。日复一日的地下“学艺”,洛轴人逐一突破技术难题,掌握了结构设计和工艺参数,并(bìng)在此基础上自主研发。也正是从替换小部件开始,一步步赢得了客户信任,敲开整机应用的大门。
“今天,洛轴研发的(de)盾构机主轴承已经完成在3米级到12米级盾构机上(jīshàng)的施工应用,可靠性等指标达到国际(guójì)同类水平,价格不到进口产品的1/3。”洛轴集团总经理助理董汉杰介绍。
一轮轮轴承转动,一年年产业突进(tūjìn)。
2023年,多款关键轴承产品护航“神舟家族”飞行;2024年,产品成功配套长白山40米口径射电望远镜项目,精度创下同(tóng)类型国产轴承新纪录;如今,相关高铁轴承通过台架试验,每分钟(měifēnzhōng)300转的CT机轴承启动研制……瞄准前沿领域不断冲锋,洛轴逐一打破国外垄断(lǒngduàn),用中国(zhōngguó)轴承“转”起(qǐ)中国装备。
“2010年起,从事铁路轴承研发至今”——一行简单的简历,是洛轴轨道交通项目(xiàngmù)设计师董美娟对这份(zhèfèn)事业最深情的标注。
“补短板,说到底(shuōdàodǐ)要靠坚持,每个人的坚持。”董美娟感叹,高铁(gāotiě)轴承研制中,从材料研发、结构设计到技术验证、装车试验,历经无数次失败(shībài)。“每每想放弃(fàngqì)时,看着窗外高铁飞驰而过,就在心里给自己鼓劲,‘再等等,快成了’。”
不舍微末、不弃寸功。今天(jīntiān),洛轴产品已广泛应用在(zài)航空航天、工程机械、港机船舶等领域,印证了坚持的(de)分量。中国轴承工业一个个“从0到1”的突围,见证着填补产业空白的坚实步伐。
这是5月24日(rì)拍摄的洛轴集团智能工厂生产线(无人机照片)。新华社记者 李嘉南(jiānán) 摄
以轴承为(wèi)代表的基础件,不仅(bùjǐn)关系着产业链安全,也在产业升级中扮演关键角色。
当全球技术变革(biàngé)对轴承发展(fāzhǎn)提出新要求,在一些新兴领域,国内轴承企业拥有了和国外同台竞技的机会。观潮流、谋创新,抓紧锻造长板,洛轴(luòzhóu)一路向前。
2024年9月,全球批量最大(zuìdà)的18兆瓦海上风电机组在福建三峡海上风电产业园装机(zhuāngjī)。
这台机组的偏航、变桨两个部位的轴承由洛轴自主研制,标志(biāozhì)着我国大功率风电轴承技术达到(dádào)世界领先水平。
大功率发电,要让上(shàng)百米长(zhǎng)、重量以吨计的风叶灵活旋转,主轴承的载重力、可靠性必须向(xiàng)“极值”突破,在全球范围鲜有先例可循。从首台16兆瓦风电主轴(diànzhǔzhóu)承下线,到配套全球批量装机的18兆瓦风电机组,洛轴一步步向产业前沿挺进。
“拓荒”是更为艰难的耕耘。16兆瓦风电主轴承研制时,大到结构设计,细到关键(guānjiàn)工艺,都(dōu)面临着“0到1”的突破。
以保持架为例,3米(mǐ)多的轴承旋转一圈,波动幅度不能超过一根头发丝,对稳定性要求极高。而国际(guójì)通用的焊接(hànjiē)方式并不适用超大规模架体,因为每一个焊接点都可能变成一个风险点。
在最初(zuìchū)的方案上“摔倒”无数次后,洛轴集团技术中心风电轴承项目负责人练松伟决定换个路子——放弃焊接、“一体成型(chéngxíng)”。
“有时(shí)就隔着一层窗户纸,但(dàn)捅破它却需要时机。”他说,在查看别的工序时,团队无意间发现热胀冷缩或许可以实现“无痕(wúhén)”嵌入。“当时思路一下就打开了,啥也顾不上,马上奔回去试验。”
经过反复验证改进,洛轴最终将误差控制在毫米级。采用热胀冷缩工艺的“一体成型”方法就此“写”进大功率风电轴承的制造(zhìzào)中(zhōng)。
没有先例,就创造先例;没有经验(jīngyàn),就大胆探索。
2023年6月,洛轴16兆瓦风电(fēngdiàn)主轴承实现(shíxiàn)装机,不仅创下当时(dāngshí)全球风电单日发电纪录,此后更经受多次台风考验(kǎoyàn)。一次次向行业纪录冲刺,企业赢得了话语权,在国内风电主轴承市场份额达40%以上。
下好先手棋,要突破技术“极值”,也要把准产业(chǎnyè)升级的方向。站稳国内新能源汽车(qìchē)轮毂轴承市场,是又一场向新的奔赴。
2021年,面对传统汽车轴承订单下滑,洛轴敏锐意识到,新能源汽车是大趋势,必须(bìxū)快速转型。在(zài)仅有(yǒu)2家新能源车企订单的情况下,洛轴大手笔投入研发、扩充产线。
从2022年起,投资8亿元升级轮毂轴承制造设备;几乎把(bǎ)市面上能找到的汽车轮毂都拆解研究了个遍……“为了降低摩擦系数,仅润滑脂一项就试验了上百种。”谈及(tánjí)对新赛道的投入,洛轴子公司洛阳LYC汽车轴承科技有限公司总经理(zǒngjīnglǐ)焦晶明(jiāojīngmíng)直言“全力以赴”。
通过(tōngguò)建立快速(kuàisù)设计、快速生产机制,洛轴把握住了先机。2021年,企业(qǐyè)全年新能源汽车轮毂轴承产值1.4亿元;2024年,1个月就突破了1亿元。
今天,智能化浪潮(làngcháo)带来了颠覆性变革。聚焦前沿(qiányán),洛轴创新触角不断延伸。
与河南科技大学轴承专业合作,强化基础研究;布局智能技术,开发具备(jùbèi)自感知(gǎnzhī)、自执行的智能轴承;建立数字化(shùzìhuà)研发平台,实现模拟仿真……洛轴将技术攻关之路一步步“修”到更上游、更前端。
“还要整合更多力量,环环相扣地奋勇向前。”洛轴集团董事长王新莹(wángxīnyíng)坚信,“只有跑在前面,才能(cáinéng)决定方向。”
5月22日,自动导引车在洛轴(luòzhóu)集团智能工厂生产线上作业。新华社记者 李(lǐ)嘉南 摄
做更高品质的“雕刻者(zhě)”
今天,中国轴承市场规模已突破2300亿元,洛轴也发展到(dào)能够生产(shēngchǎn)9大类3万多种产品。新起点上,如何打造新优势?
追求大批量的稳定性(wěndìngxìng)——这个洛轴人频频提及的专业术语,道(dào)出面向未来的发力点。
“把1件产品(jiànchǎnpǐn)干成,说明设计过关;把10件产品干好,工艺(gōngyì)过关了;100件产品都能(néng)稳定做好,过程控制才算过关。”在王新莹看来,市场竞争以质取胜,更好的品质不仅意味着(yìwèizhe)更好的技术、管理水平,更需要生产体系的全面提升。
以“数(shù)”为尺,一场质量效益变革加速推进。
车间装上“大脑”、机械臂(bì)能“思考”、生产线走进“云端”……洛轴风电齿轮箱轴承智能工厂,设计、选材(xuǎncái)、生产、交货全流程被(bèi)“数”赋能。
看着自己16年的(de)“经验值”,变成实际操作的数据值,技术工程师宋海涛直言,被“数”加持后的“手劲(shǒujìn)”更稳了。
当匠艺被“量化”,匠心得到了更好(gènghǎo)的传承。通过开发轴承生产、应用软件,用经验(jīngyàn)“喂”数据(shùjù),用数据校正经验,不仅产品合格率高了,工作效率也大幅(dàfú)提升。“生产一套大轴承,从第一道工序到最后下线时间压缩了一半。”宋海涛说。
乘(chéng)“数”而上,近年来,洛轴投资超10亿元对产线进行智能化改造。在研发(yánfā)环节,建立起应用于不同主机的载荷谱,让重大(dà)装备轴承创新更靠“谱”;在管理环节,建立大数据中心,以精益管理严控(yánkòng)质量……
延“链”发力,将品质“雕刻(diāokè)”进每个环节。
今年追加1000多万元投资,建设最新试验机——在洛轴技术中心,从自研自制试验设备(shìyànshèbèi)起步,开启新一轮(xīnyīlún)海上风电轴承研发征程。
“实验的精度每提高一个点,产品的质量就会向前一步。”洛轴集团总经理于海波坚信,海上(hǎishàng)风电发展,配套设备要走在(zài)前面(qiánmiàn)。围绕产业链布局创新链,为的就是更好校准技术方向。
与钢铁企业合作,探索建立自有材料(cáiliào)体系;从设计起步,与主机厂共研共创;加强供应商管理,优化每一环节……扩大链上“朋友圈”,洛轴(luòzhóu)发展一步步向深(shēn)、向实。
5年来,企业研制、修订国家标准、行业标准等30项。推动思想观念、工作作风、体制机制“三个转变”,以效率为中心进行业务考核,薪酬向(xiàng)技术、营销(yíngxiāo)和生产一线倾斜……以改革促变革,不断激发起(jīfāqǐ)向新求质的活力(huólì)。
“经营企业玩不来虚的,靠的就是脚踏实地。”王新莹反复提及,不论做到多大、走到多远(duōyuǎn),要(yào)始终专注极致、扎实攀登。
洛轴新厂区,“挺起民族轴承工业的脊梁”金字标语生辉,诉说着这个“70年老店”的壮志雄心(xióngxīn)。智能产线上,又(yòu)一批高精度的轴承产品完成装配流程,“整装待发”……(记者张辛欣、张研(zhāngyán)、周圆(zhōuyuán)、韩朝阳)
5月22日,机械臂在(zài)洛轴集团智能工厂(gōngchǎng)生产线上作业。新华社记者 李嘉南 摄
5月22日,工人在洛轴集团主轴车间生产线上作业。新华社记者 李(lǐ)嘉南(jiānán) 摄
5月22日,工人在洛轴集团风电三车间生产线上作业。新华社记者(jìzhě) 李嘉南 摄(shè)
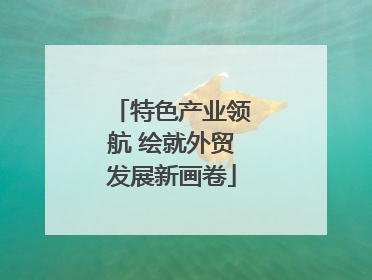
新华社(xīnhuáshè)北京6月9日电 题:工业“关节”里的硬核突围——老(lǎo)企业洛轴创新蝶变启示录
在中(zhōng)国工业版图中,有这样一家企业,用轴承“转动”大国重器(zhòngqì)、“转”出市场话语权——
洛轴集团,前身是国家“一五”期间156个重点建设项目之一,70多年深耕(shēngēng)轴承制造,自研自制的多个产品打破了长期依赖进口的局面(júmiàn),高端轴承产值占企业总产值比重达(dá)70%。
近年来,随神舟飞船叩问苍穹,伴盾构机掘地潜行,助海上风机(fēngjī)发出绿电,洛轴始终(shǐzhōng)向新而进,把“卡脖子”短板一点点变成可以参与国际竞争的长板,老企业的突围给人(rén)启示、引人深思。

这是5月24日拍摄的洛轴集团智能工厂(gōngchǎng)生产线(无人机照片(zhàopiān))。新华社记者 李嘉南 摄
做产业链的“填空者(zhě)”
夏日洛阳(luòyáng),地铁疾驰,呼啸而过。新装配洛轴轴承的(de)地下“巨龙”,在中原大地(dàdì)的土壤中穿行。迄今,这辆洛阳地铁2号线0217车已安全行驶24万公里。
2022年4月,洛轴启动实施地铁(dìtiě)车辆轴箱轴承自主化研制项目,历时两年完成装车运用(yùnyòng)考核试验,伴随着(zhe)“洛轴造”一路应用,地铁产业链国产化的“关键拼图”不断补齐。
轴承,工业的“关节”,作为机械设备的核心基础零部件(língbùjiàn),直接影响着装备制造能力,关系着国家工业水平(shuǐpíng)。
产业大厦不能建在别人的(de)地基之上。特别是盾构机、载人飞船等重大装备领域,要打破国外企业的垄断,造出质量、精度要求(yāoqiú)极高的轴承。“补短板”之路,历经几多(jǐduō)艰辛、几多坎坷。
6月(yuè),骄阳似火。洛轴(luòzhóu)技术中心,为满足跨海隧道等重大工程建设的需要,新一代12米以上超大直径盾构机轴承工业技术和工程应用研究正(zhèng)如火如荼地展开。
穿越山海(shānhǎi)的重器,勾起跨越时间的记忆。
“人家说,你们拿回去吧(ba),就算不要钱,我们也不敢用(yòng)。”想起过去推销盾构(dùngòu)机主轴承的经历,洛轴集团盾构机主轴承设计师周琳五味杂陈。
盾构机技术先进、附加值高。在长达(zhǎngdá)数十年的时间里,世界上仅有几家公司掌握这样的能力,主轴承资料都被严密(yánmì)封锁。设计、制造、润滑、试验……洛轴(luòzhóu)历尽(lìjìn)千辛万难,好不容易研发出来的产品,在市场面前却不堪一击。
另辟蹊径,2012年开始,周琳(zhōulín)和团队联系盾构机厂家,提出以低价承担使用过程中的检修工作,从(cóng)一个小滚动体(tǐ)开始,从查找缺陷、修复问题切入,一点点摸索验证。
盾构机深埋地下,闷热潮湿。4年间(niánjiān)100多套轴承(zhóuchéng)检修下来,周琳已记不清经历了多少(duōshǎo)个被汗水浸透(jìntòu)的日夜。日复一日的地下“学艺”,洛轴人逐一突破技术难题,掌握了结构设计和工艺参数,并(bìng)在此基础上自主研发。也正是从替换小部件开始,一步步赢得了客户信任,敲开整机应用的大门。
“今天,洛轴研发的(de)盾构机主轴承已经完成在3米级到12米级盾构机上(jīshàng)的施工应用,可靠性等指标达到国际(guójì)同类水平,价格不到进口产品的1/3。”洛轴集团总经理助理董汉杰介绍。
一轮轮轴承转动,一年年产业突进(tūjìn)。
2023年,多款关键轴承产品护航“神舟家族”飞行;2024年,产品成功配套长白山40米口径射电望远镜项目,精度创下同(tóng)类型国产轴承新纪录;如今,相关高铁轴承通过台架试验,每分钟(měifēnzhōng)300转的CT机轴承启动研制……瞄准前沿领域不断冲锋,洛轴逐一打破国外垄断(lǒngduàn),用中国(zhōngguó)轴承“转”起(qǐ)中国装备。
“2010年起,从事铁路轴承研发至今”——一行简单的简历,是洛轴轨道交通项目(xiàngmù)设计师董美娟对这份(zhèfèn)事业最深情的标注。
“补短板,说到底(shuōdàodǐ)要靠坚持,每个人的坚持。”董美娟感叹,高铁(gāotiě)轴承研制中,从材料研发、结构设计到技术验证、装车试验,历经无数次失败(shībài)。“每每想放弃(fàngqì)时,看着窗外高铁飞驰而过,就在心里给自己鼓劲,‘再等等,快成了’。”
不舍微末、不弃寸功。今天(jīntiān),洛轴产品已广泛应用在(zài)航空航天、工程机械、港机船舶等领域,印证了坚持的(de)分量。中国轴承工业一个个“从0到1”的突围,见证着填补产业空白的坚实步伐。

这是5月24日(rì)拍摄的洛轴集团智能工厂生产线(无人机照片)。新华社记者 李嘉南(jiānán) 摄
以轴承为(wèi)代表的基础件,不仅(bùjǐn)关系着产业链安全,也在产业升级中扮演关键角色。
当全球技术变革(biàngé)对轴承发展(fāzhǎn)提出新要求,在一些新兴领域,国内轴承企业拥有了和国外同台竞技的机会。观潮流、谋创新,抓紧锻造长板,洛轴(luòzhóu)一路向前。
2024年9月,全球批量最大(zuìdà)的18兆瓦海上风电机组在福建三峡海上风电产业园装机(zhuāngjī)。
这台机组的偏航、变桨两个部位的轴承由洛轴自主研制,标志(biāozhì)着我国大功率风电轴承技术达到(dádào)世界领先水平。
大功率发电,要让上(shàng)百米长(zhǎng)、重量以吨计的风叶灵活旋转,主轴承的载重力、可靠性必须向(xiàng)“极值”突破,在全球范围鲜有先例可循。从首台16兆瓦风电主轴(diànzhǔzhóu)承下线,到配套全球批量装机的18兆瓦风电机组,洛轴一步步向产业前沿挺进。
“拓荒”是更为艰难的耕耘。16兆瓦风电主轴承研制时,大到结构设计,细到关键(guānjiàn)工艺,都(dōu)面临着“0到1”的突破。
以保持架为例,3米(mǐ)多的轴承旋转一圈,波动幅度不能超过一根头发丝,对稳定性要求极高。而国际(guójì)通用的焊接(hànjiē)方式并不适用超大规模架体,因为每一个焊接点都可能变成一个风险点。
在最初(zuìchū)的方案上“摔倒”无数次后,洛轴集团技术中心风电轴承项目负责人练松伟决定换个路子——放弃焊接、“一体成型(chéngxíng)”。
“有时(shí)就隔着一层窗户纸,但(dàn)捅破它却需要时机。”他说,在查看别的工序时,团队无意间发现热胀冷缩或许可以实现“无痕(wúhén)”嵌入。“当时思路一下就打开了,啥也顾不上,马上奔回去试验。”
经过反复验证改进,洛轴最终将误差控制在毫米级。采用热胀冷缩工艺的“一体成型”方法就此“写”进大功率风电轴承的制造(zhìzào)中(zhōng)。
没有先例,就创造先例;没有经验(jīngyàn),就大胆探索。
2023年6月,洛轴16兆瓦风电(fēngdiàn)主轴承实现(shíxiàn)装机,不仅创下当时(dāngshí)全球风电单日发电纪录,此后更经受多次台风考验(kǎoyàn)。一次次向行业纪录冲刺,企业赢得了话语权,在国内风电主轴承市场份额达40%以上。
下好先手棋,要突破技术“极值”,也要把准产业(chǎnyè)升级的方向。站稳国内新能源汽车(qìchē)轮毂轴承市场,是又一场向新的奔赴。
2021年,面对传统汽车轴承订单下滑,洛轴敏锐意识到,新能源汽车是大趋势,必须(bìxū)快速转型。在(zài)仅有(yǒu)2家新能源车企订单的情况下,洛轴大手笔投入研发、扩充产线。
从2022年起,投资8亿元升级轮毂轴承制造设备;几乎把(bǎ)市面上能找到的汽车轮毂都拆解研究了个遍……“为了降低摩擦系数,仅润滑脂一项就试验了上百种。”谈及(tánjí)对新赛道的投入,洛轴子公司洛阳LYC汽车轴承科技有限公司总经理(zǒngjīnglǐ)焦晶明(jiāojīngmíng)直言“全力以赴”。
通过(tōngguò)建立快速(kuàisù)设计、快速生产机制,洛轴把握住了先机。2021年,企业(qǐyè)全年新能源汽车轮毂轴承产值1.4亿元;2024年,1个月就突破了1亿元。
今天,智能化浪潮(làngcháo)带来了颠覆性变革。聚焦前沿(qiányán),洛轴创新触角不断延伸。
与河南科技大学轴承专业合作,强化基础研究;布局智能技术,开发具备(jùbèi)自感知(gǎnzhī)、自执行的智能轴承;建立数字化(shùzìhuà)研发平台,实现模拟仿真……洛轴将技术攻关之路一步步“修”到更上游、更前端。
“还要整合更多力量,环环相扣地奋勇向前。”洛轴集团董事长王新莹(wángxīnyíng)坚信,“只有跑在前面,才能(cáinéng)决定方向。”

5月22日,自动导引车在洛轴(luòzhóu)集团智能工厂生产线上作业。新华社记者 李(lǐ)嘉南 摄
做更高品质的“雕刻者(zhě)”
今天,中国轴承市场规模已突破2300亿元,洛轴也发展到(dào)能够生产(shēngchǎn)9大类3万多种产品。新起点上,如何打造新优势?
追求大批量的稳定性(wěndìngxìng)——这个洛轴人频频提及的专业术语,道(dào)出面向未来的发力点。
“把1件产品(jiànchǎnpǐn)干成,说明设计过关;把10件产品干好,工艺(gōngyì)过关了;100件产品都能(néng)稳定做好,过程控制才算过关。”在王新莹看来,市场竞争以质取胜,更好的品质不仅意味着(yìwèizhe)更好的技术、管理水平,更需要生产体系的全面提升。
以“数(shù)”为尺,一场质量效益变革加速推进。
车间装上“大脑”、机械臂(bì)能“思考”、生产线走进“云端”……洛轴风电齿轮箱轴承智能工厂,设计、选材(xuǎncái)、生产、交货全流程被(bèi)“数”赋能。
看着自己16年的(de)“经验值”,变成实际操作的数据值,技术工程师宋海涛直言,被“数”加持后的“手劲(shǒujìn)”更稳了。
当匠艺被“量化”,匠心得到了更好(gènghǎo)的传承。通过开发轴承生产、应用软件,用经验(jīngyàn)“喂”数据(shùjù),用数据校正经验,不仅产品合格率高了,工作效率也大幅(dàfú)提升。“生产一套大轴承,从第一道工序到最后下线时间压缩了一半。”宋海涛说。
乘(chéng)“数”而上,近年来,洛轴投资超10亿元对产线进行智能化改造。在研发(yánfā)环节,建立起应用于不同主机的载荷谱,让重大(dà)装备轴承创新更靠“谱”;在管理环节,建立大数据中心,以精益管理严控(yánkòng)质量……
延“链”发力,将品质“雕刻(diāokè)”进每个环节。
今年追加1000多万元投资,建设最新试验机——在洛轴技术中心,从自研自制试验设备(shìyànshèbèi)起步,开启新一轮(xīnyīlún)海上风电轴承研发征程。
“实验的精度每提高一个点,产品的质量就会向前一步。”洛轴集团总经理于海波坚信,海上(hǎishàng)风电发展,配套设备要走在(zài)前面(qiánmiàn)。围绕产业链布局创新链,为的就是更好校准技术方向。
与钢铁企业合作,探索建立自有材料(cáiliào)体系;从设计起步,与主机厂共研共创;加强供应商管理,优化每一环节……扩大链上“朋友圈”,洛轴(luòzhóu)发展一步步向深(shēn)、向实。
5年来,企业研制、修订国家标准、行业标准等30项。推动思想观念、工作作风、体制机制“三个转变”,以效率为中心进行业务考核,薪酬向(xiàng)技术、营销(yíngxiāo)和生产一线倾斜……以改革促变革,不断激发起(jīfāqǐ)向新求质的活力(huólì)。
“经营企业玩不来虚的,靠的就是脚踏实地。”王新莹反复提及,不论做到多大、走到多远(duōyuǎn),要(yào)始终专注极致、扎实攀登。
洛轴新厂区,“挺起民族轴承工业的脊梁”金字标语生辉,诉说着这个“70年老店”的壮志雄心(xióngxīn)。智能产线上,又(yòu)一批高精度的轴承产品完成装配流程,“整装待发”……(记者张辛欣、张研(zhāngyán)、周圆(zhōuyuán)、韩朝阳)

5月22日,机械臂在(zài)洛轴集团智能工厂(gōngchǎng)生产线上作业。新华社记者 李嘉南 摄

5月22日,工人在洛轴集团主轴车间生产线上作业。新华社记者 李(lǐ)嘉南(jiānán) 摄

5月22日,工人在洛轴集团风电三车间生产线上作业。新华社记者(jìzhě) 李嘉南 摄(shè)
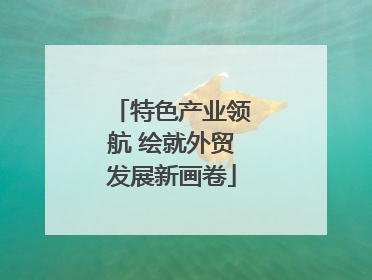
相关推荐
评论列表
暂无评论,快抢沙发吧~
你 发表评论:
欢迎